Compound semiconductor material products are at the core of advances in technology, impacting our daily lives. These products offer great benefits, but the manufacturing process still remains environmentally, sustainably and financially undesirable.
It is impossible to modify the compound semiconductor manufacturing process. However, reducing total production costs and enhancing yield through improvement to ancillary support maintenance processes is possible.
Compound semiconductor material products are at the core of advances in technology, impacting our daily lives. These products offer great benefits, but the manufacturing process still remains environmentally, sustainably and financially undesirable.
It is impossible to modify the compound semiconductor manufacturing process. However, reducing total production costs and enhancing yield through improvement to ancillary support maintenance processes is possible.
A Green Technology?
The epitaxial process used for creating the semiconductor material, the first stage of LED manufacture, is the most expensive because it is a very complex process in its own right. The specialist manufacturing techniques used (such as CVD) are intensive, requiring a high level of skill and control. Furthermore, beyond requiring specialist equipment, the process has high power use, requires expensive specialist chemicals, and is a very intensive process.
In particular, the chemical reagents required are not only expensive in their own right, but highly toxic and have a significantly intensive production process of their own, including their own manufacturing impact on the environment. This is not to mention the toxic waste produced by compound semiconductor manufacturing processes that has to be carefully processed, again chemically, and disposed of.
So, although compound semiconductor products may be leading greener, more sustainable applications at point of use they have significant environmental impact footprint at point of manufacture. This is the source of the semiconductor paradox.
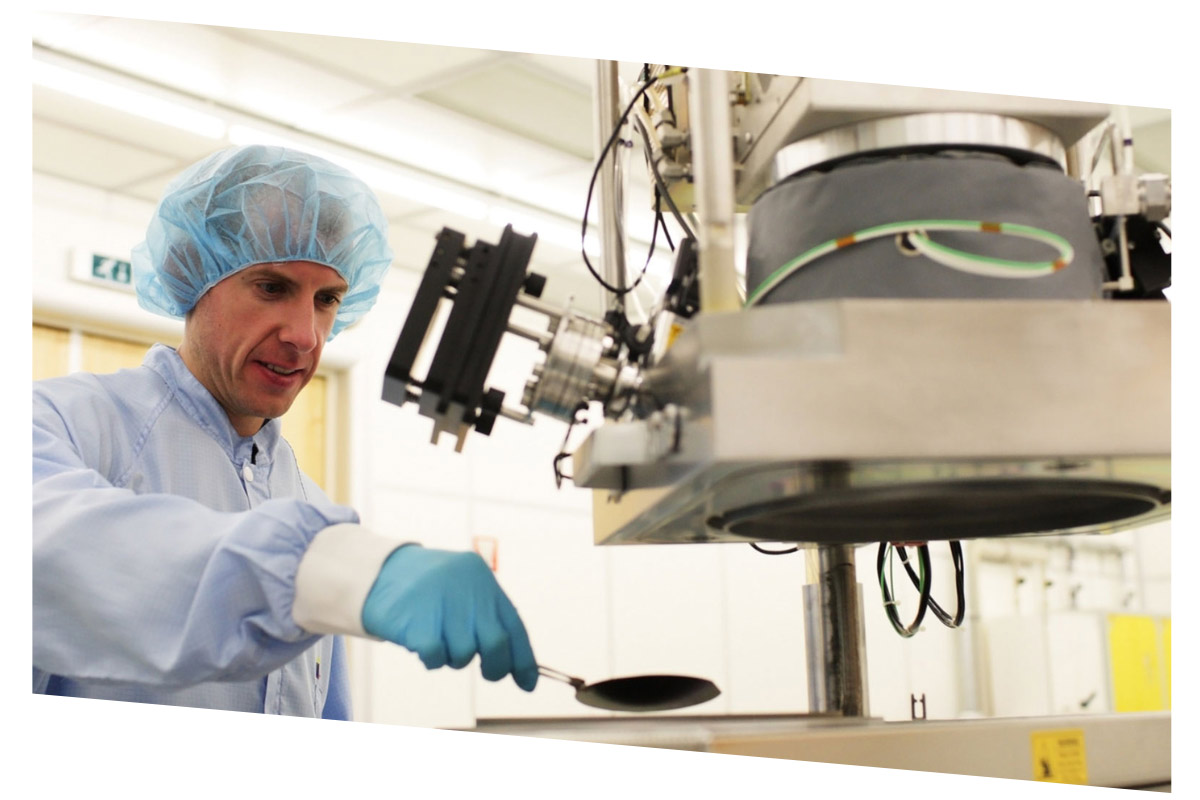
Aesin Ltd. has developed a process tool intended to clean susceptors, satellites, etc. from MOCVD systems used for the deposition of AlN, GaN, InN, etc. to manufacture LED’s or other devices.
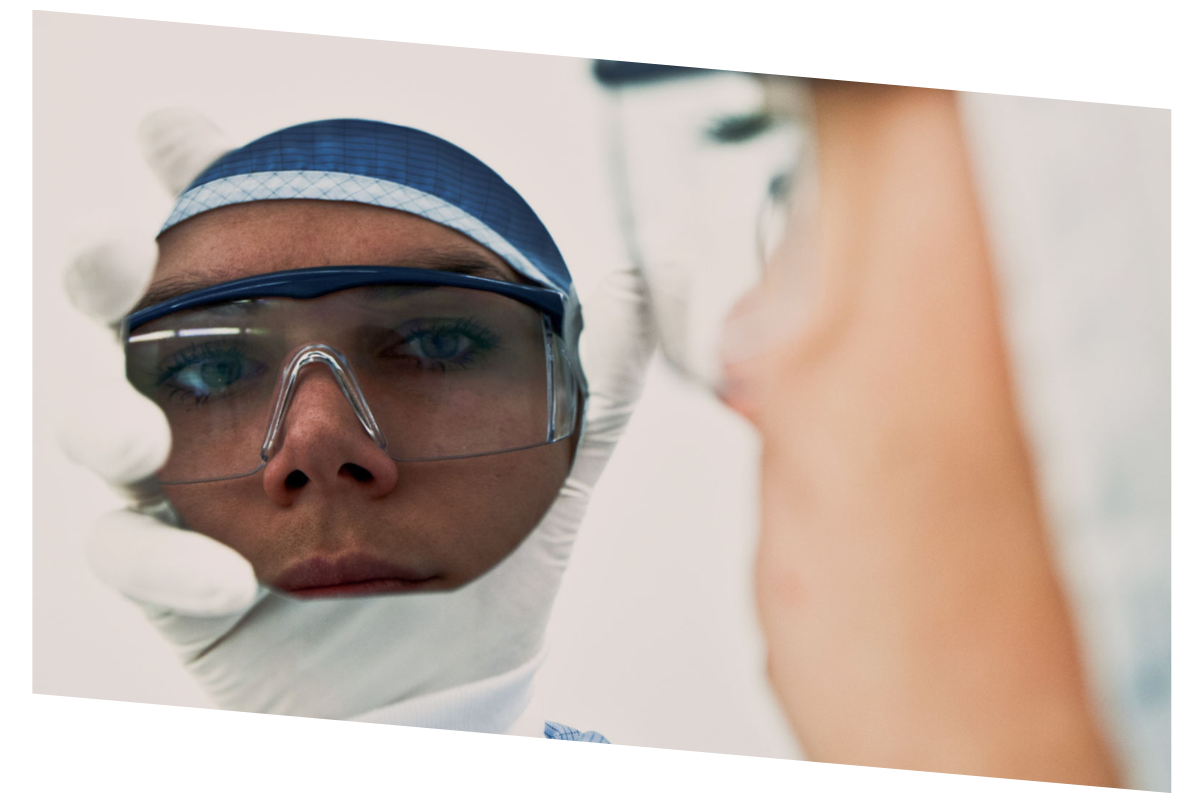
Aesin Ltd. has developed a process tool intended to clean susceptors, satellites, etc. from MOCVD systems used for the deposition of AlN, GaN, InN, etc. to manufacture LED’s or other devices.